Контрольная работа: ОСНОВЫ СТРОЕНИЯ И СВОЙСТВА МАТЕРИАЛОВ. ФАЗОВЫЕ ПРЕВРАЩЕНИЯ
Координационное число в кристаллографии, число ближайших к данному атому или иону соседних одинаковых атомов или ионов в кристалле.
Дата добавления на сайт: 23 апреля 2025
Теория к 1 ДИДАКТИЧЕСКАЯ ЕДИНИЦА
«ОСНОВЫ СТРОЕНИЯ И СВОЙСТВА МАТЕРИАЛОВ. ФАЗОВЫЕ ПРЕВРАЩЕНИЯ»
Тема задания
1. Структура материала
Координационное число в кристаллографии, число ближайших к данному атому или иону соседних одинаковых атомов или ионов в кристалле. Прямые линии, соединяющие центры ближайших атомов или ионов в кристалле, образуют координационный многогранник, в центре которого находится данный атом. Одному и тому же К. ч. могут соответствовать разные многогранники. В структурах
алмаза
,
кремния
,
германия
,
сфалерита
К. ч. равно 4, а координационный многогранник — тетраэдр. В структуре NaCI каждый ион Na окружен шестью ионами Cl, а каждый ион Cl — шестью ионами Na, т. е. для обоих типов ионов К. ч. равно 6, многогранник — октаэдр. В структуре
флюорита
CaF2 для ионов Са К. ч. равно 8, многогранник — куб; для ионов F К. ч. равно 4, многогранник — тетраэдр. Наивысшее возможное К. ч. равно 12, что характерно для металлов с плотнейшей кубической или гексагональной упаковкой. Для металлов с объёмно-центрированной решёткой К. ч. равно 8. Для полупроводниковых кристаллов, не имеющих уплотнений упаковки атомов, характерны К. ч., равные 4 или 6.
2. Пластическая деформация и механические свойства металлов
Полигонизация - перестройка и упорядочивание дислокационной структуры металлов. Полигонизация приводит к образованию субзёренных границ. при горячей обработке металлов
Возврат (отдых) стали – нагрев до 200 – 400o, отжиг для уменьшения или снятия наклепа.
С повышением температуры диффузия атомов увеличивается и в металле начинают развиваться процессы, приводящие его к более равновесному состоянию. Это явление возврата (200 – 400).
Первая стадия возврата – отдых, наблюдается при невысоком нагреве. При отдыхе происходит уменьшение количества вакансий, уменьшение плотности дислокаций, частичное снятие напряжений.
Вторая стадия возврата – полигонизация, деление зерен на части – полигоны (субзерна).
Полигонизация происходит в результате скольжения и переползания дислокаций, вследствие чего дислокации одного знака образуют «стенки», разделяющие зерна на полигоны. При возврате заметных изменений в микроструктуре не наблюдается, металл сохраняет волокнистое строение. При этом твердость и прочность несколько понижаются, а пластичность возрастает.
Рекристаллизацией называется процесс образования и роста новых зерен при нагреве наклепанного металла до определенной температуры. Этот процесс протекает в две стадии. Различают рекристаллизацию первичную (обработки) и собирательную.
Рекристаллизация первичная (обработки) заключается в образовании зародышей и росте новых равновесных зерен с неискаженной кристаллической решеткой. Количество новых зерен постепенно увеличивается и, в конечном счете, в структуре не остается старых деформированных зерен.
Собирательная рекристаллизация – вторая стадия рекристаллизационного процесса заключается в росте образовавшихся новых зерен.
Рекристаллизационный отжиг. Этот вид отжига производится с целью устранения наклепа холоднодефор-мированного металла.
Рекристаллизационный отжиг стали (рекристаллизация) - нагрев до температур 500 – 550o; отжиг для снятия внутренних напряжений – нагрев до температур 600 – 700o. Эти виды отжига снимают внутренние напряжения металла отливок от неравномерного охлаждения их частей, также в заготовках, обработанных давлением (прокаткой, волочением, штамповкой) с использованием температур ниже критических. Вследствиии рекристаллизационного отжига из деформированных зерен вырастают новые кристаллы, ближе к равновесным, поэтому твердость стали снижается, а пластичность, ударная вязкость увеличиваются. Чтобы полностью снять внутренние напряжения стали нужна температура не менее 600o .
Охлаждение после выдержки при заданной температуре должно быть достаточно медленным: вследствие ускоренного охлаждения металла вновь возникают внутренние напряжения.
3. Процесс кристаллизации и фазовые превращения в сплавах. Основные типы диаграмм состояния
I. Сплавы, образующие гетерогенные структуры
Гетерогенные структуры («механическая смесь») образуются тогда, когда компоненты сплава не вступают в химическое взаимодействие и не растворяются друг в друге в твердом состоянии. Этот тип образуется при сплавлении компонентов с большой разницей атомных радиусов и значительным различием электрохимических свойств. Чем больше эти различия, тем меньше растворимость компонентов друг в друге.
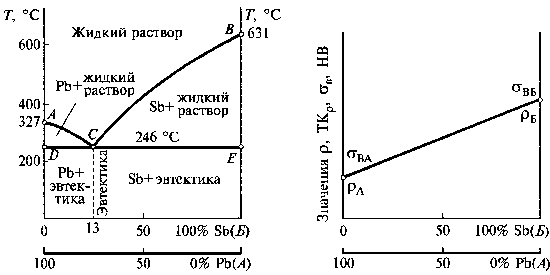
II. Сплавы с неограниченной растворимостью компонентов в твердом состоянии
В твердом растворе замещения атомы растворенного компонента замещают часть атомов растворителя в узлах его кристаллической решетки. С неограниченной растворимостью образуются твердые растворы тогда, когда сплавляемые компоненты имеют одинаковый тип кристаллической решетки, близкие параметры решетки и сходные по строению оболочки валентных электронов в атомах. Если эти условия не соблюдаются, образуется раствор с ограниченной растворимостью.
В твердом растворе внедрения атомы растворенного компонента располагаются в междоузлиях кристаллической решетки растворителя. Такие твердые растворы образуются, когда атомы растворяемого компонента имеют малый радиус
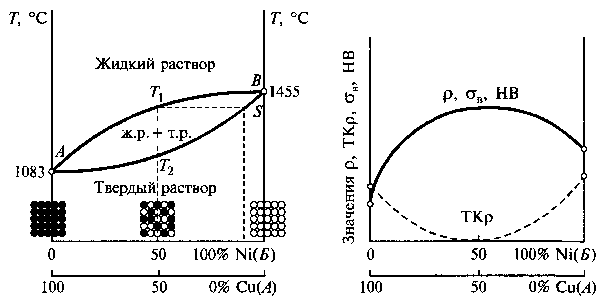
Неоднородность состава внутри кристалла называют внутрикристаллической (или дендритной) ликвацией (под ликвацией вообще понимают неоднородность системы по химическому составу). Ликвация —свойство сплавов распадаться при переходе из жидкого в твердое состояние на составные части или отдельные соединения, которые имеют различные точки плавления. Эту ликвацию можно в значительной мере устранить отжигом.
III.Сплавы с ограниченной растворимостью компонентов в твердом состоянии
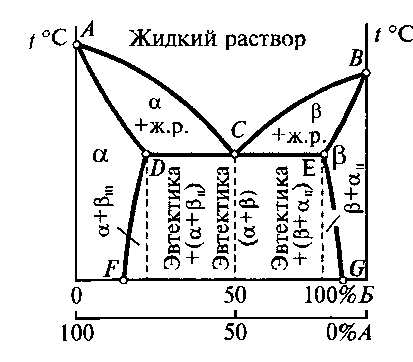

У этих типов сплавов в той части, где имеют место однофазные области твердых растворов (области - и -фазы), механические и электрические свойства проявляют криволинейную концентрационную зависимость, как это наблюдалось у сплавов, образующих твердые растворы с неограниченной растворимостью компонентов в твердом состоянии. В двухфазных областях свойства изменяются аддитивно, как это наблюдалось у сплавов, образующих гетерогенные структуры.
IV. Сплавы, образующие химические соединения
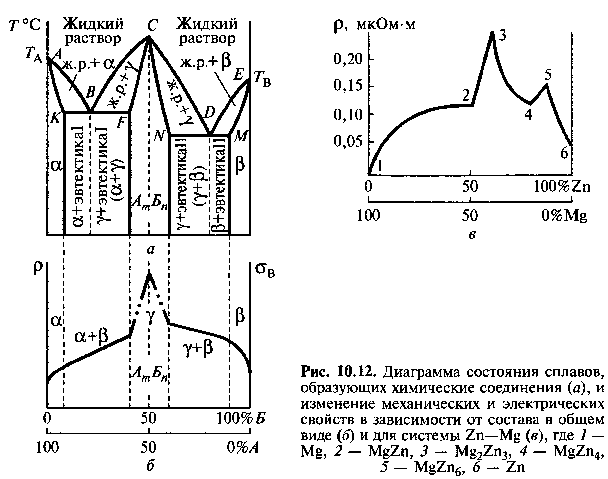
Сплавы, образующие химические соединения одного металла с другим, называются интерметаллидами.
В месте соединения двух диаграмм можно выделить точку перелома или острие вершины – точку С, соответствующую концентрациям компонентов А и Б, при которых образуется устойчивое химическое соединение АmБn. Эту точку (C) называют сингулярной.
4. Диаграмма ?железо-цементит?
ОСНОВЫ ТЕРМИЧЕСКОЙ ОБРАБОТКИ И ПОВЕРХНОСТНОГО УПРОЧНЕНИЯ СПЛАВОВ
Тема задания
5 Основы термической обработки
Цель нагрева – получение Аустенита
Цель охлаждения – получение желаемой структуры (Перлит – Сорбит – Троостит – Мартенсит при увеличении скорости остывания Аустенита)
6 Отжиг и нормализация стали
Рекристаллизационный отжиг стали (рекристаллизация) - нагрев до температур 500 – 550o; отжиг для снятия внутренних напряжений – нагрев до температур 600 – 700o. Эти виды отжига снимают внутренние напряжения металла отливок от неравномерного охлаждения их частей, также в заготовках, обработанных давлением (прокаткой, волочением, штамповкой) с использованием температур ниже критических. Вследствие рекристаллизационного отжига из деформированных зерен вырастают новые кристаллы, ближе к равновесным, поэтому твердость стали снижается, а пластичность, ударная вязкость увеличиваются.
Охлаждение после выдержки при заданной температуре должно быть достаточно медленным: вследствии ускоренного охлаждения металла вновь возникают внутренние напряжения.
Диффузионный отжиг стали (гомогенизация) применяется тогда, когда сталь имеет внутрикристаллическую ликвацию (неоднородность системы по химическому составу). Выравнивание состава в зернах аустенита достигается диффузией углерода и других примесей в твердом состоянии, наряду с самодиффузией железа. По результатам отжига, сталь становится однородной по составу (гомогенной), поэтому диффузионный отжиг называет также гомогенизацией.
Диффузионный отжиг стали обычно приводит к слишком сильному укрупнению зерна, что следует исправлять последующим полным отжигом (на мелкое зерно).
Полный отжиг стали связан с фазовой перекристаллизацией, измельчением зерна при температурах точек АС1 и АС2. Назначение его – улучшение структуры стали для облегчения последующей обработки резанием, штамповкой или закалкой, а также получение мелкозернистой равновесной перлитной структуры готовой детали. Для полного отжига сталь нагревают на 30-50 o выше температуры линии GSK и медленно охлаждают.
После отжига избыточный цементит (в заэвтектоидных сталях) и эвтектоидный цементит имеют форму пластинок, поэтому и перлит называют пластинчатый
При отжиге стали на пластинчатый перлит заготовки оставляют в печи до охлаждения, чаще всего при частичном подогреве печи топливом, чтобы скорость охлаждения была не больше 10-20o в час.
Отжигом также достигается измельчение зерна. Крупнозернистая структура, например, доэвтектоидной стали, получается при затвердевании вследствие свободного роста зерен (если охлаждение отливок медленное), а также в результате перегрева стали. Эта структура называется видманштетовой (по имени австрийского астронома А. Видманштеттена, открывшего в 1808 г. такую структуру на метеорном железе). Такая структура придает низкую прочность заготовке. Структура характерна тем, что включения феррита (светлые участки) и перлита (темные участки) располагаются в виде вытянутых пластин под различными углами друг к другу. В заэвтектоидный сталях видманштетова структура характеризуется штрихообразным расположением избыточного цементита.
Таким образом, одним из результатов отжига на пластинчатый перлит является мелкозернистая структура.
Неполный отжиг стали связан с фазовой перекристаллизацией лишь при температуре точки А С1; неполный отжиг применяется после горячей обработки давлением, когда у заготовки мелкозернистая структура.
Отжиг стали на зернистый перлит применяют обычно для эвтектоидных, заэвтектоидных сталей, для повышения пластичности, вязкости стали и уменьшения ее твердости. Для получения зернистого перлита сталь нагревают выше точки АС1, затем выдерживают недолго, чтобы цементит растворился в аустените не полностью. Затем сталь охлаждают до температуры несколько ниже Ar1, выдерживают при такой температуре несколько часов. При этом частицы оставшегося цементита служат зародышами кристаллизации для всего выделяющегося цементита, который нарастает округлыми (глобулярными) кристаллитами, рассеянными в феррите.
Свойство зернистого перлита существенно отличаются от свойств пластинчатого в сторону меньшей твердости, но большей пластинчатости и вязкости. Особенно это относится к заэвтектоидной стали.
Изотермический отжиг - после нагрева и выдержки сталь быстро охлаждают до температуры несколько ниже точки А 1 , затем выдерживают при этой температуре до полного распадения аустенита на перлит, после чего охлаждают на воздухе. Применение изотермического отжига значительно сокращает время, а также повышает производительность. Например, обыкновенный отжиг легированной стали длится 13-15 ч, а изотермический – всего 4-7 ч
7 Закалка и отпуск сталей
Закаливаемость – способность повышать твердость во время закалки (зависит от С. Чем больше С в тем выше твердость)
Прокаливаемость – способность закаливаться на определенную глубину (опред. Критич. Скоростью охлаждения)
Закалка – пластинчатая структура; Отпуск – зернистая.
Отпуск – нагрев закаленной стали до температур ниже критической точки Ас1 выдержка при этой температуре с последующим охлаждением.
Низкий отпуск нагревают до 150—250 °С, выдерживают, охлаждают. Образуются мелкие частицы -карбида – мартенсит отпуска (режущий инструмент и др. сплавы высокой твердости и износостойкости)
Средний отпуск 350-450°С. Образуется тростит отпуска. (повышенная пластичность и вязкость. Все пружины, включая локомотивов)
Высокий отпуск 500–680°С. Образуется сорбит отпуска (констр. Материалы и многие детали машин: шестерни, валы, оси …)
Отжиг укрупняет зерно; закалка – измельчает: меньше зерно выше твердость.
8 Химико-термическая обработка. Поверхностная закалка
Цементация – диффузионный процесс, при котором поверхностный слой мягкой стали насыщается углеродом.
Стали, содержащие около 0,25% углерода (низкоуглеродистые 0,1–0,35% C) с небольшим количеством легирующих элементов, цементуются легко; высокое содержание легирующих элементов может препятствовать диффузии углерода.
После цементации производят закалку с низким отпуском.
Азотирование – поверхностном насыщении азотом в среде аммиака (NH3) при температурах нагрева 500–700° С. Применяется для повышения твердости, износостойкости, предела усталости, сопротивления коррозии и жаропрочности.
Азотированию могут подвергаться детали из углеродистой низко-легированной и легированной (содержат хром, молибден…) сталей, а также чугун. Чаще всего конструкционные улучшаемые стали, не содержащие алюминия
Перед Азотированием производят закалку с высоким отпуском
КОНСТРУКЦИОННЫЕ МЕТАЛЛЫ И СПЛАВЫ
Тема задания
9 Конструкционные стали
Низкоуглеродистые – до 0,25% углерода
Среднеуглеродистые 0,3–0,6% углерода
Высокоуглеродистые 0,7–1,3% углерода
По назначению: конструкционные и инструментальные.
Конструкционные: обыкновенного качества (группы А– Ст0, Ст2…, группы Б– БСт0, БСт2…, группы В–ВСт0, ВСт2…,) Номер марки характеризует механические свойства. К маркировке недораскисленных («кипящих») сталей прибавляют буквы кп: Ст1кп.
Конструкционные углеродистые качественные стали. Маркировка состоит из двузначного числа, указывающего на содержание углерода в сотых долях процента: 05, 08, 10, 75, 80 и 85.
55пп– пониженной прокаливаемоесть; 60Г, 65Г, 70Г –с повышенным содержанием марганца (около 1 %).
Буква А, стоящая в конце марки, свидетельствует об улучшенном металлургическом качестве:
Инструментальные углеродистые стали – высокоуглеродистые (содержание углерода 0,7—1,3 %),
Марки качественных сталей: У7, – У13А. буква У – сталь углеродистая, число – среднее содержание углерода в десятых долях процента, буква А – улучшенное металлургическое качество
Для изготовления мерительного, режущего и ударно-штампового инструмента.
Стали специального назначения (стали мостостроения, рельсовая, осевая, бандажная и колесная).
Сталь для мостостроения двух марок: М16С – для сварных мостовых конструкций и СтЗ – для клепаных мостов.
Сталь рельсовая М75 (0,67 - 0,80 % С) и М76 (0,69 - 0,82 % С). М75 маркируется Р50, а М76 – как Р65.
Легированные стали:
низколегированные (легирующих элементов до 2,5 %),
среднелегированные (от 2,5 до 10 %)
высоколегированные (свыше 10 %).
Маркировка.
Цифры, перед буквами, – содержание углерода в сотых долях процента, если две цифры, и в десятых долях процента, если одна цифра. Отсутствие впереди букв цифр означает, что углерода >1 %. Цифры, за буквами, – среднее содержание данного легирующего элемента в процентах. Отсутствие за буквой цифры – элемента содержится до 1 %. Стоящая в конце буква А – высококачественная сталь (если Ш – особовысококачественная).
марганец Мn – Г; кремний Si – С; хром Сг – X; никель Ni – Н; молибден Мо – М; вольфрам W – В; ванадий V – Ф; алюминий А1 – Ю; титан Ti – Т; бор В – Р; медь Сu – Д; ниобий Nb – Б.
Вначале А– хорошая обрабатываемость, Ш – шарикоподшипниковая, Р – быстрорежущая.
Венцы зубчатых передач локомотивов 30ХН3А или 45ХН с поверхностной закалкой ТВЧ
Рессоры и пружины кремнистая сталь 55С2 или 60С2 с закалкой и отпуском.
10 Чугуны
Большая часть углерода в виде графита.
Серые (СЧ 24) 24 – временное сопротивление при растяжении кгс/мм2 (пластинчатые граф. включения). Для улучшения св-ств модифицируют вводя модификаторы. (корпус редуктора, станина …)
Высокопрочные (ВЧ 50) (шаровидные граф. включения) (Коленчатые валы авто и судов, зубчатые колеса)
Ковкие (КЧ 35-10) 10 – относит. удлинение в %. (хлопьевидные граф. включения) Получают длительным графитизирующего отжига отливок из белого чугуна. (тонкостенные отливки деталей, рычаги, педали)
11 Сплавы на основе меди
Бронзы – это сплавы меди с небольшим содержанием одного или нескольких химических элементов (Sn, Si, P, Be, Cr, Mg, Cd и др.).
Маркировка: БрОЦС6-6-3 – оловянно-цинково-свинцовая бронза (Sn6%, Zn6%, Pb3%, остальное медь). Фосфор – Ф, цинк–Ц, хром–Х, бериллий–Б, цирконий–Цр, олово–О, свинец–С, кремний–К, А – алюминий, Ж – железо, никель–Н, кадмий–Кд, хром – Х …
Удельное сопротивление бронз больше, чем у чистой меди, зато выше предел прочности на разрыв (в=250–1100 МПа) и твердость (НВ=20–260МПа) и износостойкость, но меньше относительное удлинение перед разрывом ( =2–65%). Бронзы лучше обрабатываются на металлорежущих станках и обладают более высокими литейными свойствами, чем медь.
Латуни – это сплавы системы Сu—Zn с максимальным содержанием Zn от 4% до 45%. Максимальная пластичность наблюдается при содержании Zn около 37 %.
Маркировка: ЛС59-1 свинцовая латунь, содержащая Сu 59 %, свинца 1 %, остальное цинк. С– Свинец, О– олово, Ж —железо, А – алюминий, К– кремний, Мц - Марганец, Н - никель
Главная отличительная особенность латуни от чистой меди — повышенная механическая прочность при достаточно высокой пластичности. Латуни лучше, чем бронзы, обрабатываются штамповкой, глубокой вытяжкой и т. п. Они широко используются для изготовления токопроводящих винтов, гаек, шайб, шпилек, штырей, гнезд, упругих элементов и для коммутирующих узлов и штепсельных разъемов.
12 Сплавы на основе алюминия
Сплавы алюминия обладают более высокими значениями предела прочности на разрыв ов, твердости НВ, износостойкости, нагревостойкости и удельного электросопротивления , но меньшим значением относительного удлинения перед разрывом , чем чистый алюминий.
Литейные сплавы алюминия маркируют двумя буквами АЛ и цифрой, обозначающей порядковый номер сплава. К литейным алюминиевым сплавам относят сплавы следующих систем: А1–Si–Сu (АЛЗ, АЛ5, АЛ6), А1–Сu (АЛ7, АЛ19, АЛ21), А1–Mg (АЛ8, АЛ27, АЛ13). Эти сплавы обладают хорошими литейными свойствами, свариваемостью и удовлетворительными механическими свойствами/
Cплавы алюминия с кремнием (и небольшими добавками Mg и Мn), их называют силуминами (например, АЛ2, АЛ4, АЛ9). Для получения мелкозернистой структуры и улучшения механических свойств в силумины добавляют 0,05–0,08% натрия. Такие сплавы называют модифицированными.
Деформируемые сплавы алюминия подразделяют на сплавы, не упрочняемые термической обработкой[АМц (Mn 1,0—1,6 %, остальное Al): отожженный упрочненный АМг5 (Mg 4,8-5,8, Mn 0,5-0,8 %, остальное Al) АД31 (Mg 0,4-0,9, Si 0,3-0,7 %, остальное Al) закаленный и искусственно состаренный],
и сплавы, упрочняемые термической обработкой.[ Д16 (Си 4,5, Mg 1,5, Mn 0,6 %, остальное Al): отожженный закаленный после старения наклепанный АВ (Си 0,2-0,6, Mg 0,45-0,90, Mn 0,15-0,35, Si = 0,5-1,2 %, остальное Al) В95 (Си 1,4-2,0, Mg 1,8-2,8, Mn 0,2-0,6, Si < 0,5, Zn 5,0-7,0, Cr 0,1—0,25 %, остальное Al) закаленный и отпущенный AK4-1 ((Си 1,9-2,5%, Mg 1,4-1,8, Si < 0,35, Fe 0,8-1,5, Ni 1,0-1,5, Ti 0,02—0,1 %, остальное Al) закаленный и состаренный].
Сплавы, не упрочняемые термической обработкой, имеют высокую пластичность, из них получают изделия холодной штамповкой.
Альдрей – Электротехнический сплав (Mg 0,3-0,5, Si 0,4-0,7, Fe 0,2–0,3 %, остальное Al)
ЭЛЕКТРОТЕХНИЧЕСКИЕ МАТЕРИАЛЫ
Тема задания
13 Диэлектрические материалы
14 Проводниковые материалы
15 Полупроводниковые материалы
16 Магнитные материалы